Juxiang Primary Crusher for concrete and Metal
Double Cylinder Primary Crusher
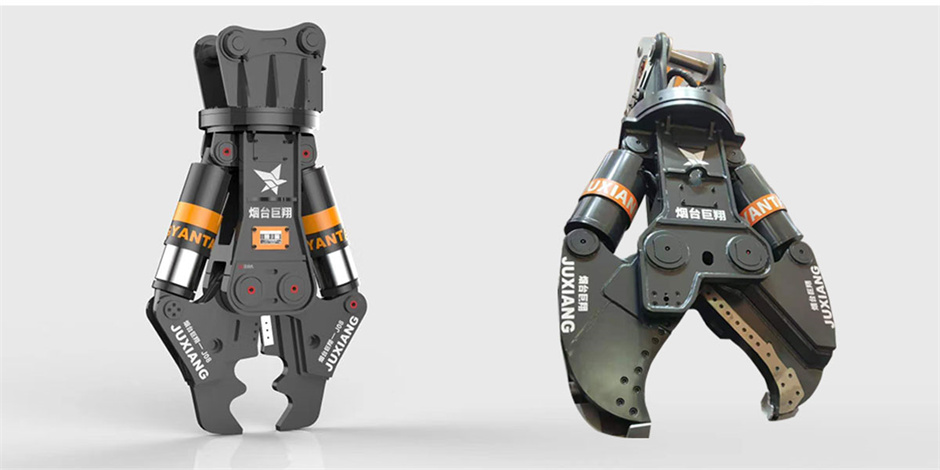
Product advantages
Model |
Unit |
HS04B |
HS06B |
HS08B |
HX10B |
HS14B |
Dead Weight |
kg |
630 |
1500 |
2300 |
2977 |
4052 |
Max Opening |
mm |
335.5 |
540 |
500 |
660 |
801 |
Height |
mm |
1521 |
2050 |
2380 |
2600 |
2700 |
Weith |
mm |
864 |
1175 |
1370 |
1600 |
1700 |
The active Length of Blade |
mm |
286 |
348 |
486 |
578 |
736 |
Rotation Mode |
360° Ball Colliding Rotation |
360° Hydraulic |
||||
Pressure |
bar |
235 |
300 |
320 |
320 |
320 |
Root Crushing Force |
t |
81 |
138 |
171 |
330 |
387 |
Middle Crushing Force |
t |
50 |
80 |
102 |
189 |
218 |
Fore-end Crushing Force |
t |
32 |
53 |
75 |
127 |
147 |
Suitable Excavator |
t |
5-8 |
15-18 |
20-25 |
28-35 |
38-50 |
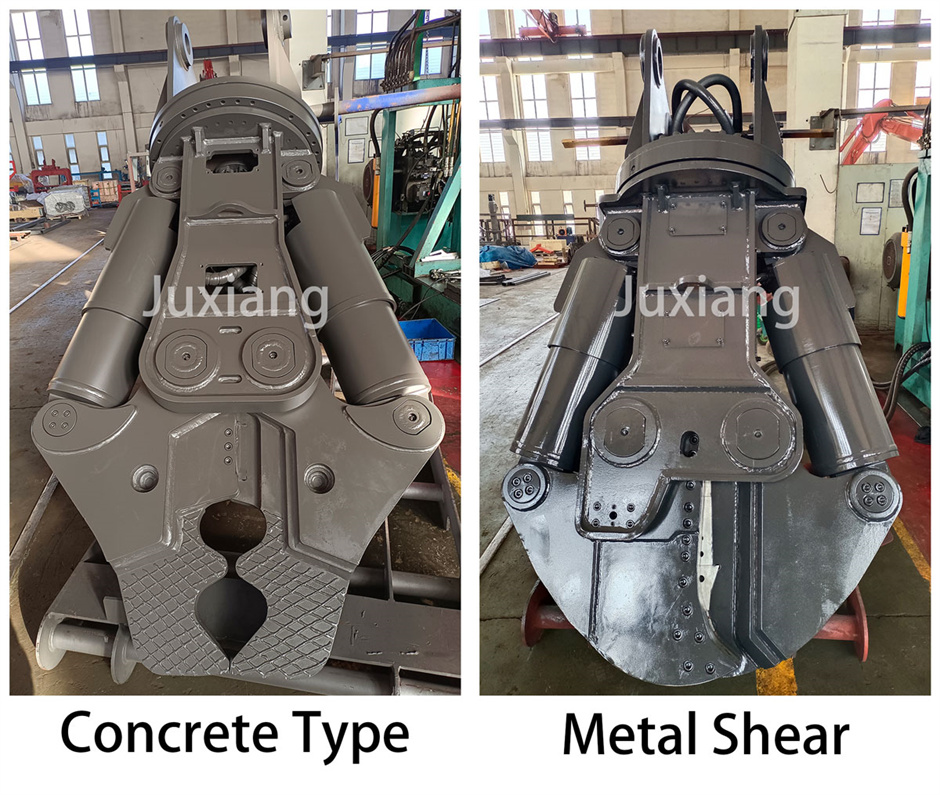
Concrete Type Dual- Cylinder Crusher
A dual-cylinder crushing clamp, also known as a twin-cylinder pulverizer, is an engineering machinery device used for dismantling and crushing hard materials such as concrete structures and rocks. Its distinctive feature is the incorporation of two hydraulic cylinders. These cylinders generate powerful force through a hydraulic system, enabling efficient crushing and dismantling tasks.
Dual-cylinder crushing clamps are commonly employed in construction sites, demolition projects, quarrying operations, and similar environments. They are utilized for demolishing concrete walls, floor slabs, rocks, and other hard materials. These clamps can be mounted on machinery like excavators or loaders, and their operations, such as opening and closing, are controlled through hydraulic mechanisms.
Due to their robust crushing capability and efficient performance, dual-cylinder crushing clamps find widespread use in projects requiring the dismantling of hard materials.
1.Metal Type Dual- Cylinder Steel Shear
A dual-cylinder steel shear is a type of hydraulic machinery used for cutting and processing steel materials. It features two hydraulic cylinders that generate powerful force to efficiently cut through steel beams, plates, and other metal structures. These shears are commonly used in industries such as metal recycling, construction, and demolition, where cutting and processing large steel components are necessary. Dual-cylinder steel shears are typically attached to heavy equipment like excavators and are controlled through hydraulic systems, providing precise and controlled cutting operations.
Design advantage
15-Meter Large Double-Column Boring and Milling Machining Center
This machining center performs axial hole boring and machining for the main arm, secondary arm, and auxiliary arm. It achieves a single-process formation of the largest 15-meter main arm, ensuring precise relative accuracy for various position axis holes
product display
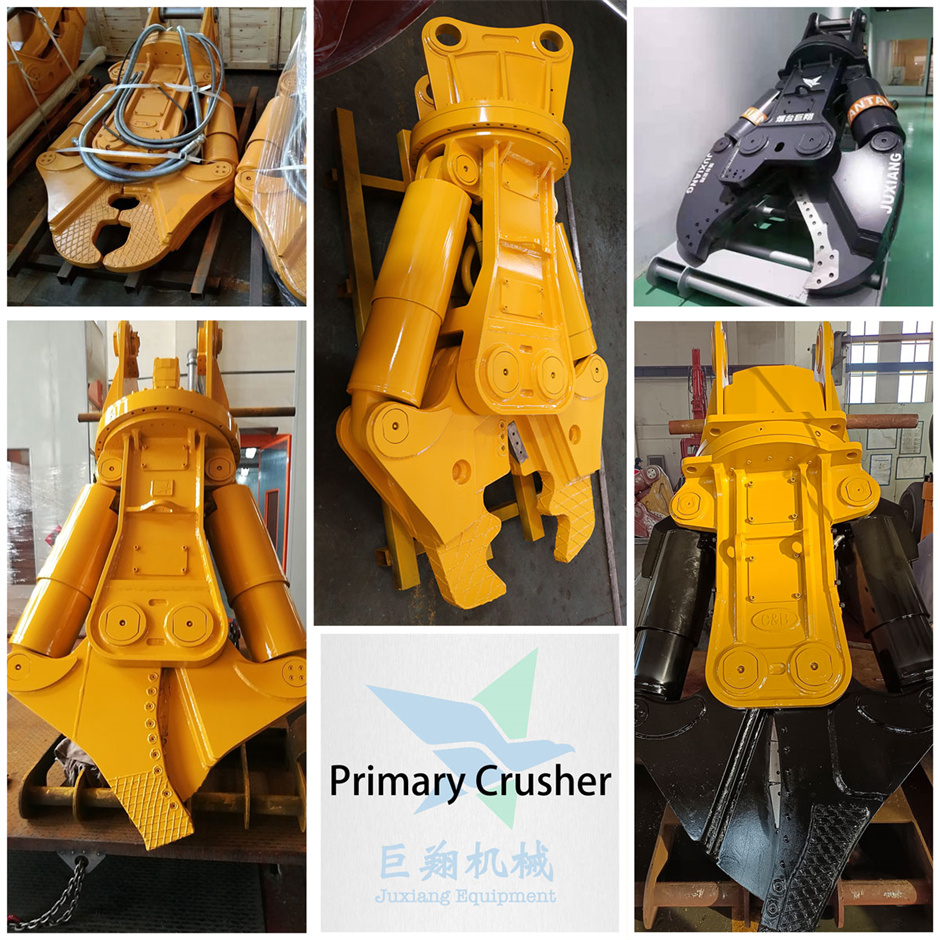
Applications
Yantai Juxiang's products boast a comprehensive range, catering to a diverse clientele. We have accumulated invaluable practical experience. Continuous refinement of our product designs based on market feedback ensures they remain well-suited and aligned with customer needs.
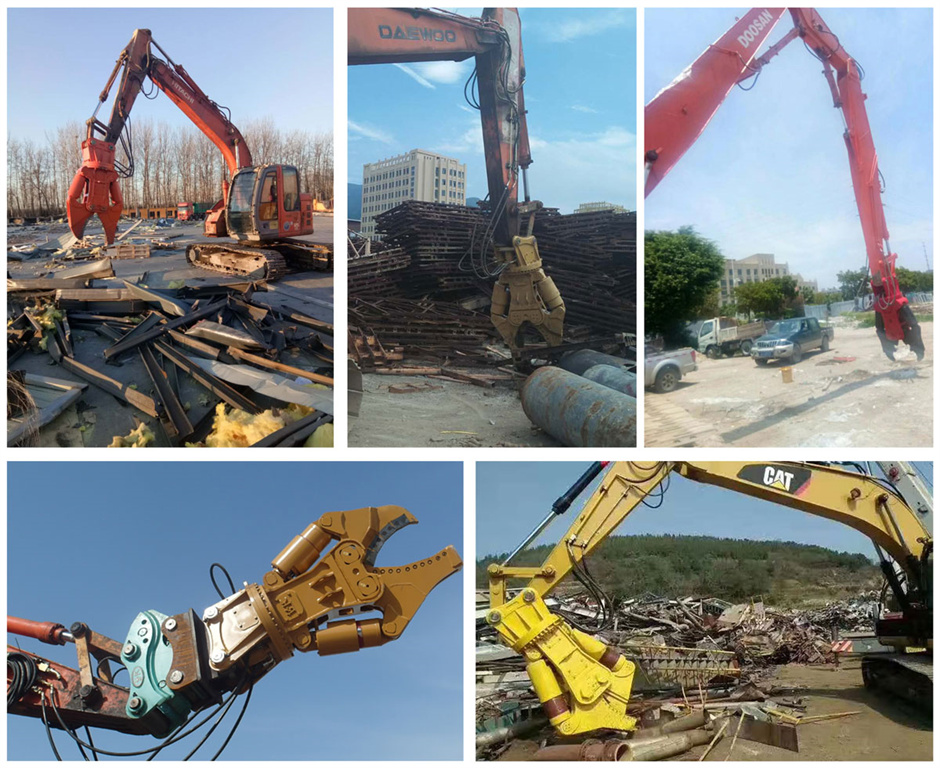

About Juxiang
Accessoryname | Warrantyperiod | Warranty Range | |
Motor | 12 months | It is free to replace the cracked shell and broken output shaft within 12 months. If the oil leakage occurs for more than 3 months, it is not covered by the claim. You must purchase the oil seal by yourself. | |
Eccentricironassembly | 12 months | The rolling element and the track stuck and corroded are not covered by the claim because the lubricating oil is not filled according to the specified time, the oil seal replacement time is exceeded, and the regular maintenance is poor. | |
ShellAssembly | 12 months | Damages caused by non-compliance with operating practices,and breaks caused by reinforce without the consent of our company,are not within the scope of claims.If Steel plate cracks within 12 months,the company will change the breaking parts;If Weld bead cracks,please weld by yourself.If you are not capable to weld,the company could weld for free,but no other expenses. | |
Bearing | 12 months | The damage caused by poor regular maintenance, wrong operation, failure to add or replace gear oil as required or is not within the scope of claim. | |
CylinderAssembly | 12 months | If the cylinder barrel is cracked or the cylinder rod is broken, the new component will be replaced free of charge. The oil leakage occurring within 3 months is not within the scope of claims, and the oil seal must be purchased by yourself. | |
Solenoid Valve/throttle /check valve /flood valve | 12 months | The coil short-circuited due to external impact and the incorrect positive and negative connection is not in the scope of claim. | |
Wiring harness | 12 months | The short circuit caused by external force extrusion, tearing, burning and wrong wire connection is not within the scope of claim settlement. | |
Pipeline | 6 months | Damage caused by improper maintenance, external force collision, and excessive adjustment of the relief valve is not within the scope of claims. | |
Bolts, foot switches, handles, connecting rods, fixed teeth, movable teeth and pin shafts are not guaranteed; The damage of parts caused by failure to use the company’s pipeline or failure to comply with the pipeline requirements provided by the company is not within the scope of claim settlement. |
1. When installing a pile driver onto an excavator, make sure the excavator’s hydraulic oil and filters are replaced after the installation and testing. This ensures the hydraulic system and parts of the pile driver work smoothly. Any impurities can damage the hydraulic system, causing issues and reducing the machine’s lifespan. **Note:** Pile drivers demand high standards from the excavator’s hydraulic system. Check and repair thoroughly before installation.
2. New pile drivers need a break-in period. For the first week of use, change the gear oil after half a day to a day’s work, then every 3 days. That’s three gear oil changes within a week. After this, do regular maintenance based on working hours. Change the gear oil every 200 working hours (but no more than 500 hours). This frequency can be adjusted depending on how much you work. Also, clean the magnet each time you change the oil. **Note:** Don’t go longer than 6 months between maintenance.
3. The magnet inside mainly filters. During pile driving, friction creates iron particles. The magnet keeps the oil clean by attracting these particles, reducing wear. Cleaning the magnet is important, about every 100 working hours, adjusting as needed based on how much you work.
4. Before starting each day, warm up the machine for 10-15 minutes. When the machine has been idle, oil settles at the bottom. Starting it means the upper parts lack lubrication initially. After about 30 seconds, the oil pump circulates oil to where it’s needed. This reduces wear on parts like pistons, rods, and shafts. While warming up, check screws and bolts, or grease parts for lubrication.
5. When driving piles, use less force initially. More resistance means more patience. Gradually drive the pile in. If the first level of vibration works, there’s no need to rush with the second level. Understand, while it might be quicker, more vibration increases wear. Whether using the first or second level, if pile progress is slow, pull the pile out 1 to 2 meters. With the pile driver and excavator’s power, this helps the pile go deeper.
6. After driving the pile, wait 5 seconds before releasing the grip. This reduces wear on the clamp and other parts. When releasing the pedal after driving the pile, due to inertia, all parts are tight. This reduces wear. The best time to release the grip is when the pile driver stops vibrating.
7. The rotating motor is for installing and removing piles. Don’t use it to correct pile positions caused by resistance or twisting. The combined effect of resistance and the pile driver’s vibration is too much for the motor, leading to damage over time.
8. Reversing the motor during over-rotation stresses it, causing damage. Leave 1 to 2 seconds between reversing the motor to avoid straining it and its parts, extending their life.
9. While working, watch for any issues, like unusual shaking of oil pipes, high temperatures, or odd sounds. If you notice something, stop immediately to check. Small things can prevent big problems.
10. Ignoring small issues leads to big ones. Understanding and caring for equipment not only reduces damage but also costs and delays.