Juxiang Post Pile Vibro Hammer For Excavator use
Post pile Vibro Hammer Product parameters
Product advantages
A post type hydraulic vibro pile driver is used for driving piles into the ground. It's typically employed in construction and foundation projects to insert various types of piles, such as steel, concrete, or timber piles, into the soil or bedrock. The machine uses hydraulic power to create vibrations that help insert the pile into the ground, ensuring a secure foundation. This equipment is commonly used in the construction of buildings, bridges, retaining walls, and other structures that require strong foundational support.
1. Solved Over Heat Issue : The box adopts an open structure to ensure pressure balance and stable heat discharge in the box.
2. Dustproof design:The hydraulic rotary motor and gear are built-in, which can effectively avoid oil pollution and collision. The gears are convenient for replacement, closely matched, stable and durable.
3. Shock absorbing:It adopts high performance imported damping rubber block, which has stable quality and long service life.
4. Parker Motro: It uses original imported hydraulic motor, which is stable in efficiency and outstanding in quality.
5. Anti-relief valve:The tong cylinder has strong thrust and keeps the pressure. It is stable and reliable to ensure that the pile body is not loose and guarantee the construction safety.
6. Post design Jaw: The tong is made of Hardox400 sheet with stable performance and long service cycle.
Design advantage
Design Team: Juxiang have a design team of over 20 people, utilizing 3D modeling software and physics simulation engines to evaluate and improve the performance of products during the early stages of design.
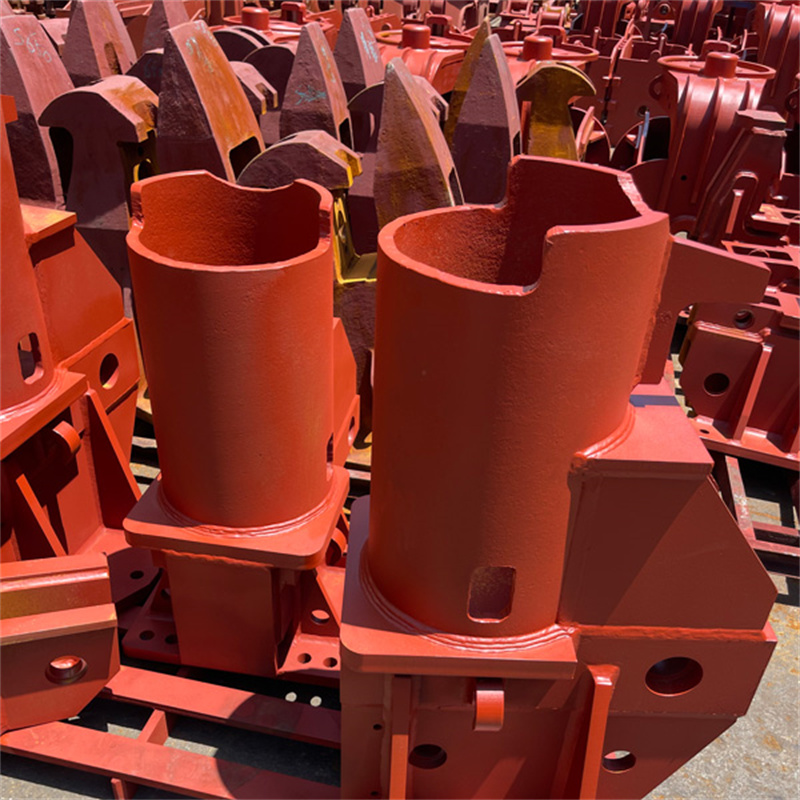
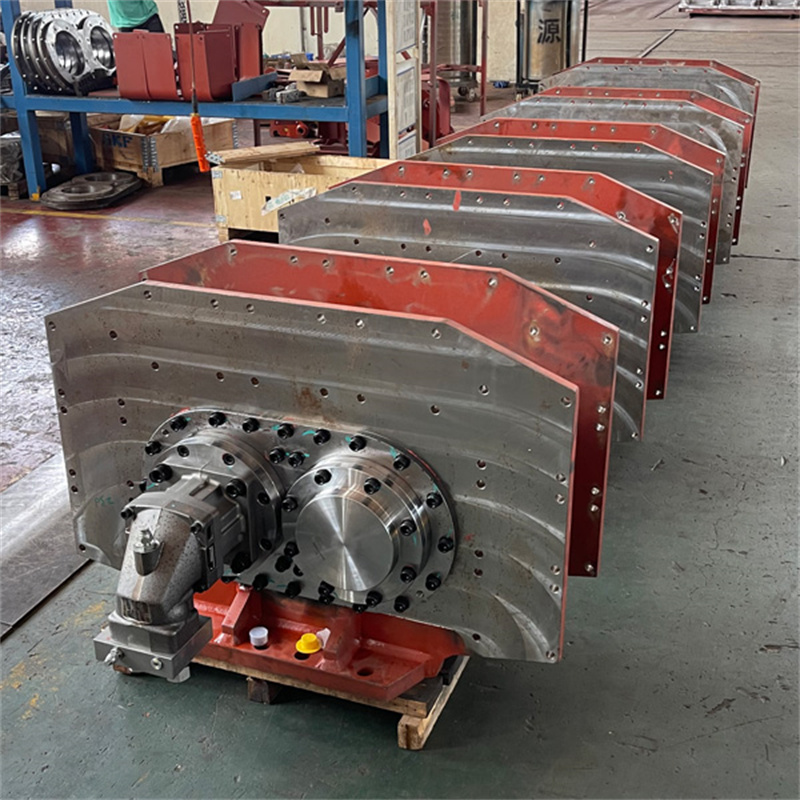
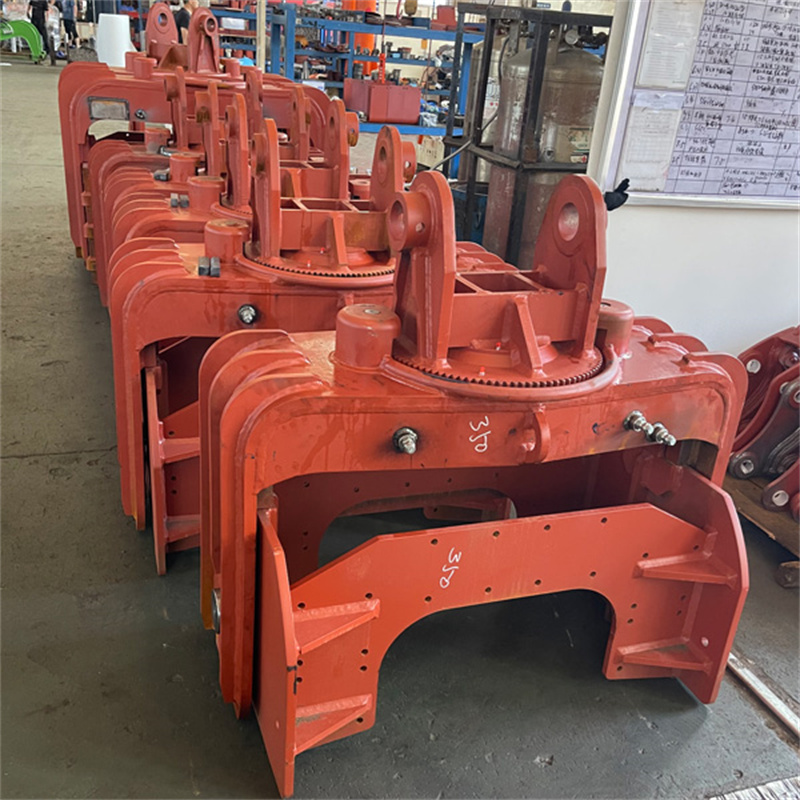
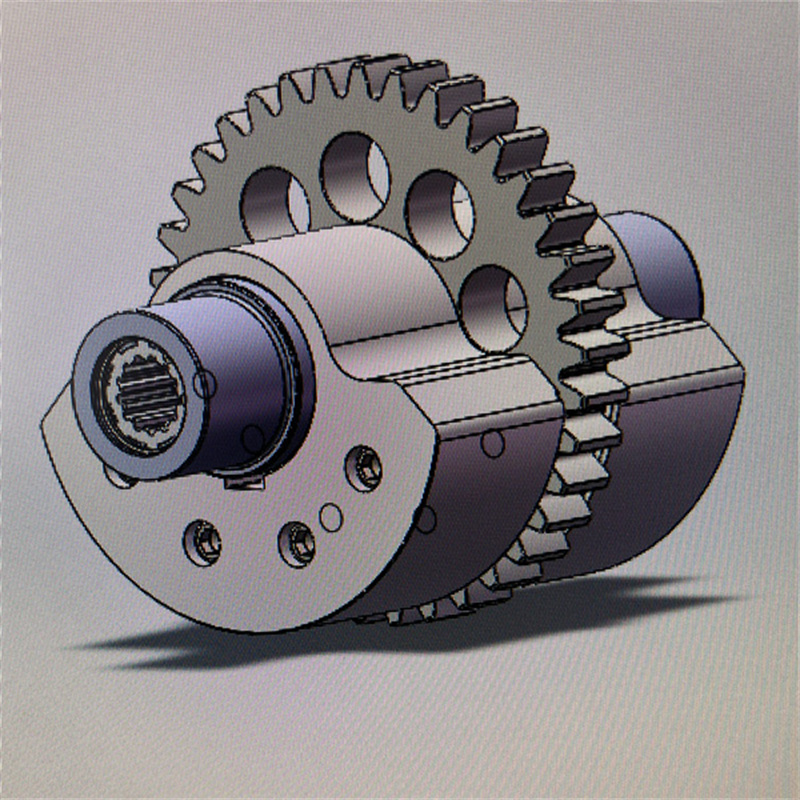
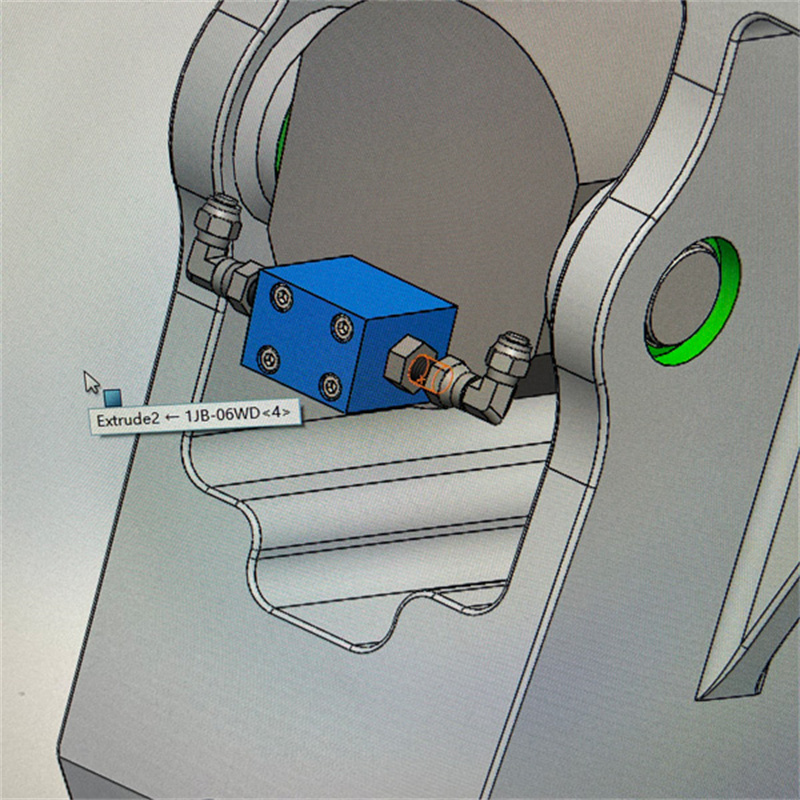
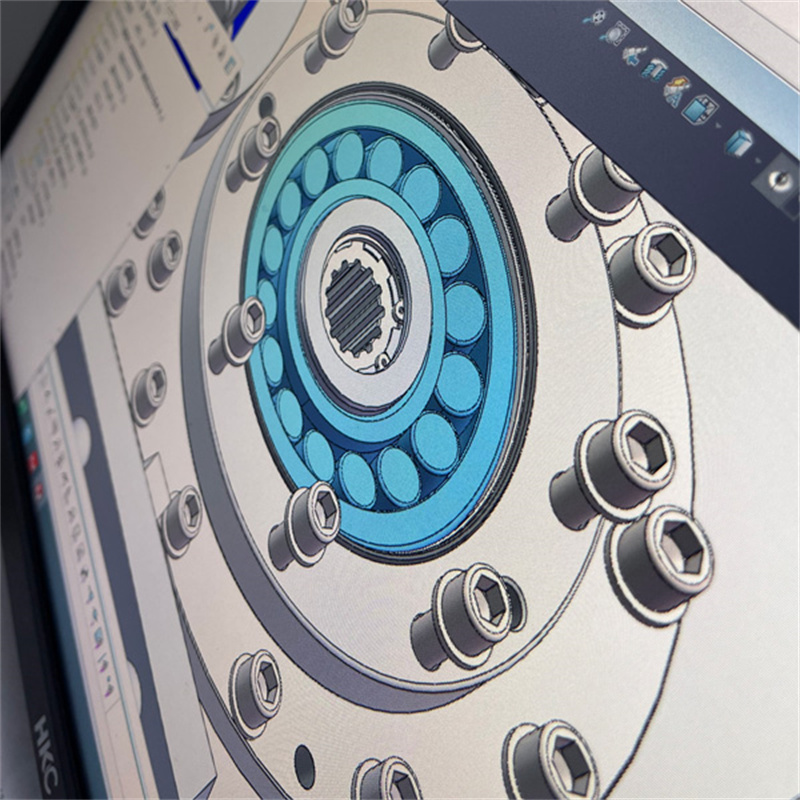
product display
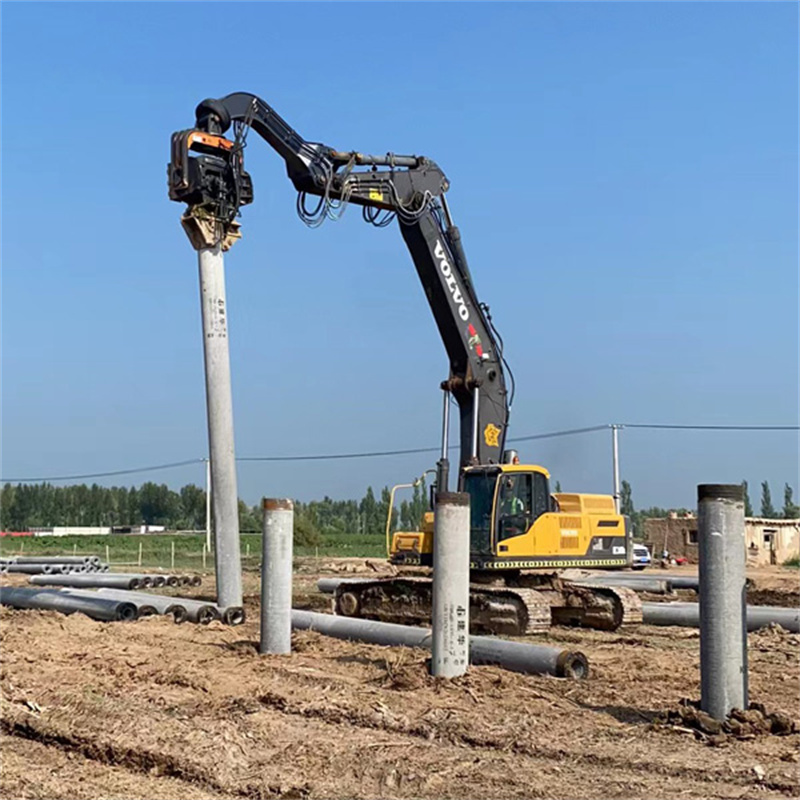
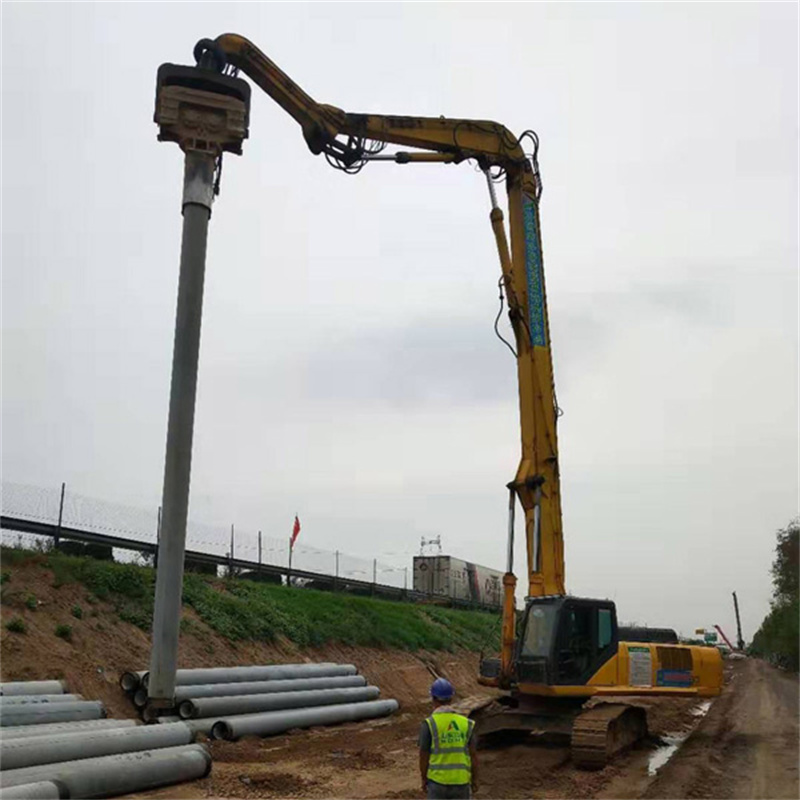
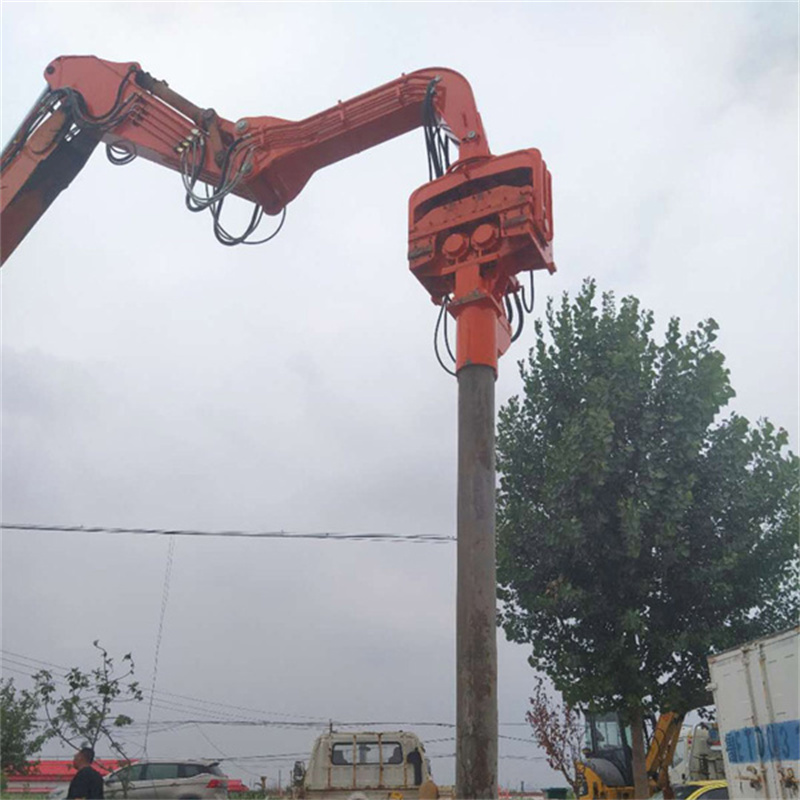
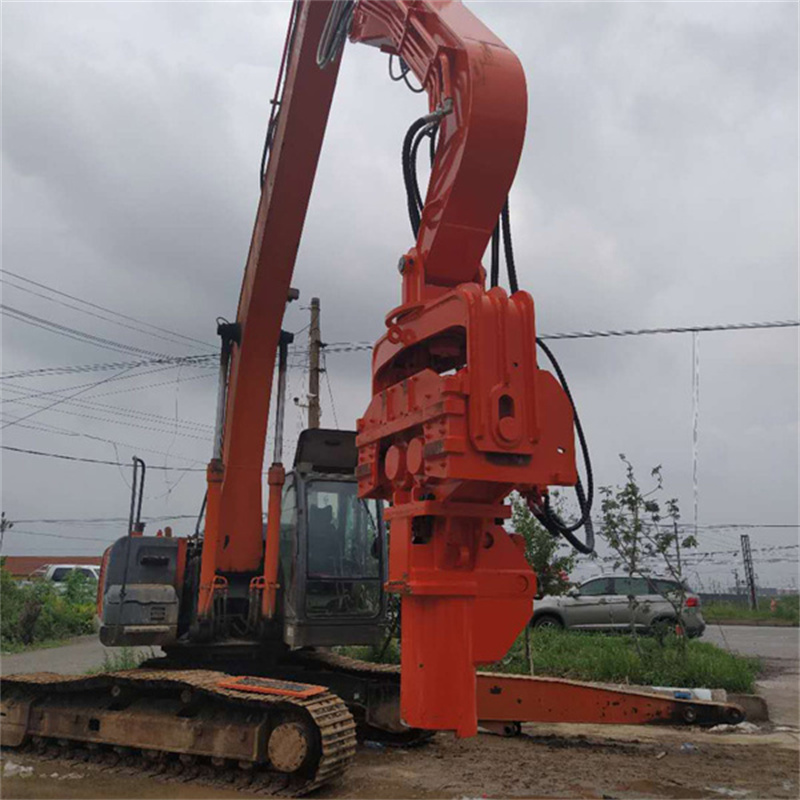
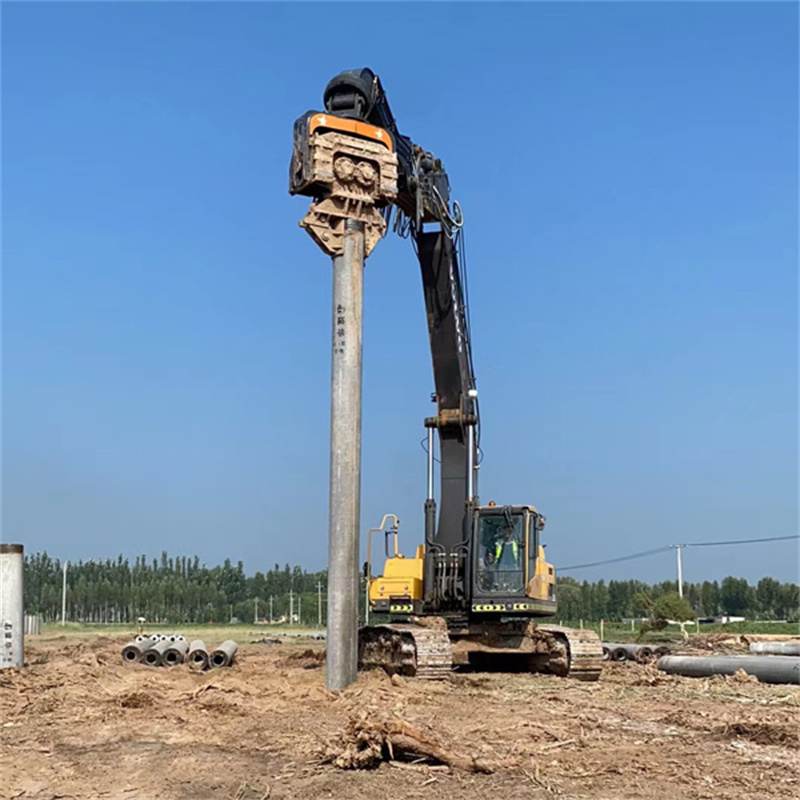
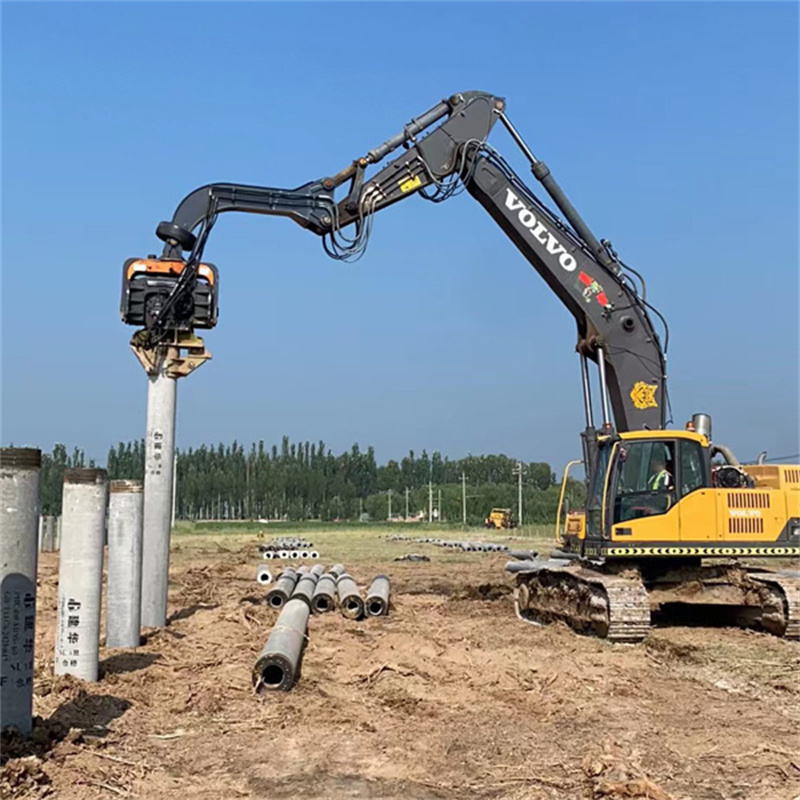
Applications
Our product is suitable for excavators of various brands and we have established long-term and stable partnerships with some well-known brands.

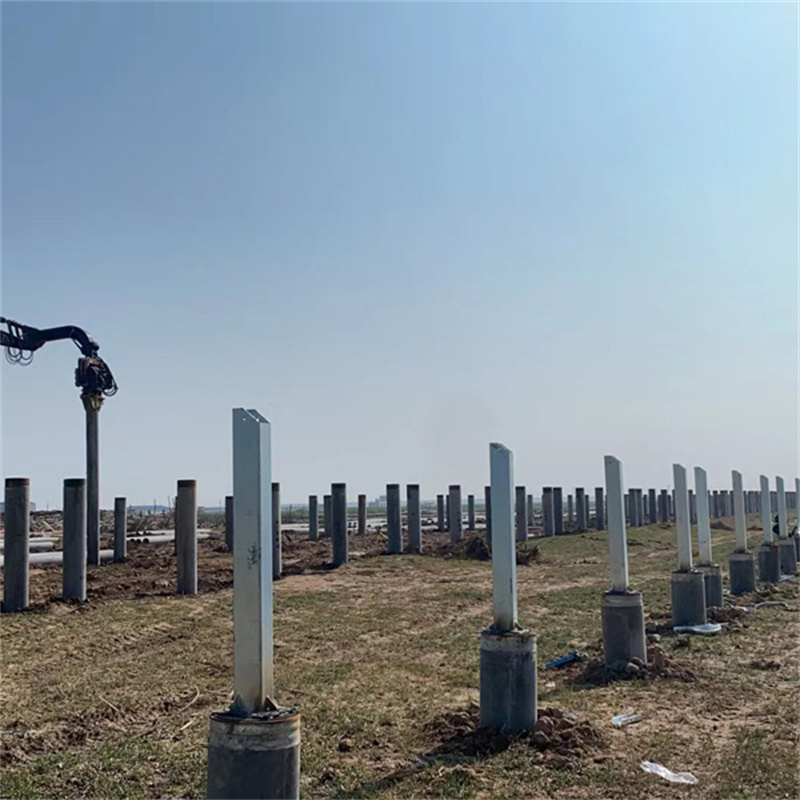
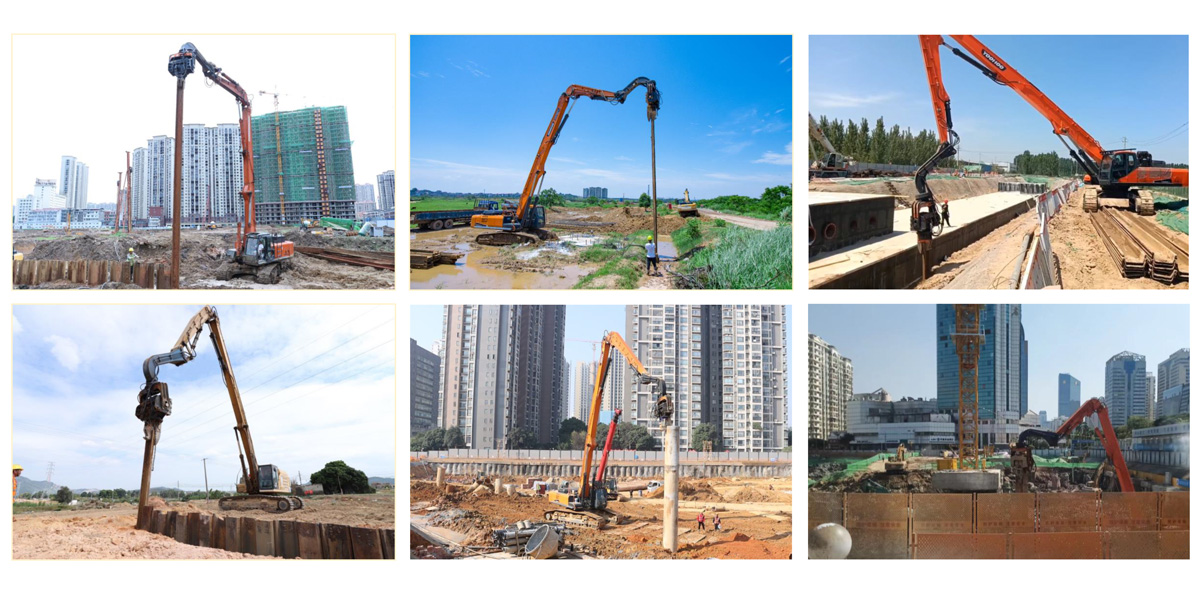
Construction Techniques for Photovoltaic Piles
1. **Site Analysis:** Conduct a thorough site analysis to understand soil composition, water tables, and environmental conditions. This informs the choice of piling method and materials.
2. **Pile Design:** Design the piles to withstand the specific load of solar panels and environmental factors like wind and snow. Consider factors like pile type (driven, drilled, screw piles), length, and spacing.
3. **Pile Installation:** Follow precise installation procedures based on the chosen pile type. Driven piles need accurate hammer placement, drilled piles require proper borehole drilling, and screw piles demand careful screwing into the ground.
4. **Foundation Leveling:** Ensure the pile tops are level to ensure a stable platform for the solar structure. Accurate leveling prevents uneven weight distribution on the piles.
5. **Anti-Corrosion Measures:** Apply appropriate anti-corrosion coatings to extend the life of piles, particularly if they are exposed to moisture or corrosive substances in the soil
6. **Quality Control:** Regularly monitor the piling process, especially for driven piles, to ensure they are plumb and at the correct depth. This minimizes the risk of leaning or inadequate support.
7. **Cabling and Conduit:** Plan the cable and conduit routing before securing the solar panels. Properly place cable trays or conduits to avoid damage during panel installation.
8. **Testing:** Perform load tests to validate pile capacity. This ensures the piles can bear the load of solar panels and environmental stresses.
9. **Environmental Impact:** Consider local regulations and environmental impact. Avoid disturbing sensitive habitats and comply with any required permits.
10. **Safety Measures:** Implement safety protocols during construction. Use proper personal protective equipment (PPE) and secure work areas to prevent accidents.
11. **Documentation:** Maintain accurate records of piling activities, including installation details, testing results, and any deviations from the original plan.
12. **Post-Installation Inspection:** Regularly inspect piles after installation to identify any signs of movement, settling, or corrosion. Timely maintenance can prevent larger issues.
The success of a photovoltaic pile installation lies in meticulous planning, accurate execution, and consistent quality control.
About Juxiang
Accessoryname | Warranty period | Warranty Range | |
Motor | 12 months | It is free to replace the cracked shell and broken output shaft within 12 months. If the oil leakage occurs for more than 3 months, it is not covered by the claim. You must purchase the oil seal by yourself. | |
Eccentricironassembly | 12 months | Claims do not cover situations where the moving parts and the surface they move on get stuck or damaged due to lack of proper lubrication, not following recommended oil filling and seal replacement schedules, and neglecting regular maintenance. | |
ShellAssembly | 12 months | Damages due to not following proper operating procedures and any breaks caused by reinforcing without our company’s approval are not covered by claims. If a steel plate breaks within 12 months, we will replace the damaged parts. If there are cracks in the weld bead, you can fix it yourself. If you can’t, we can do it for free, but you won’t incur any additional costs. | |
Bearing | 12 months | Damages resulting from neglecting regular maintenance, improper operation, not adding or changing gear oil as instructed, are not covered by claims. | |
CylinderAssembly | 12 months | If the cylinder casing has cracks or the cylinder rod is fractured, a new part will be provided at no cost. However, oil leakage issues within 3 months are not covered by claims and you will need to buy the replacement oil seal yourself. | |
Solenoid Valve/throttle /check valve /flood valve | 12 months | The coil short-circuited due to external impact and the incorrect positive and negative connection is not in the scope of claim. | |
Wiring harness | 12 months | Claims do not cover damages caused by external force, tearing, burning, or incorrect wire connections leading to a short circuit. | |
Pipeline | 6 months | Damages resulting from incorrect maintenance, collisions with external forces, or excessive adjustment of the relief valve are not covered by claims. | |
Bolts, foot switches, handles, connecting rods, fixed and movable teeth, and pin shafts are not covered by warranty. Damage to parts due to using pipelines not provided by the company or not following the company’s pipeline requirements is not included in claim coverage. |
1. When installing the pile driver on an excavator, change the excavator’s hydraulic oil and filters after testing to ensure smooth operation. Impurities can harm the hydraulic system. Note that pile drivers demand high standards from the excavator’s hydraulic system.
2. New pile drivers require a break-in period. Change gear oil every half to a full day’s work for the first week, and every 3 days after that. Regular maintenance depends on working hours. Change gear oil every 200 working hours (not exceeding 500 hours), adjusting based on usage. Clean the magnet each oil change. Don’t go more than 6 months without maintenance.
3. The magnet inside filters. Clean it every 100 working hours, adjusting as needed based on usage.
4. Warm up the machine for 10-15 minutes each day. This ensures proper lubrication. When starting, oil settles at the bottom. Wait about 30 seconds for oil circulation to lubricate vital parts.
5. Use less force when driving piles. Gradually drive the pile in. Using higher vibration levels wears the machine faster. If progress is slow, pull the pile out 1 to 2 meters and use the machine’s power to help it go deeper.
6. Wait 5 seconds before releasing the grip after driving the pile. This reduces wear. Release the grip when the pile driver stops vibrating.
7. The rotating motor is for installing and removing piles, not for correcting pile positions due to resistance. Using it this way can damage the motor over time.
8. Reversing the motor during over-rotation stresses it. Leave 1 to 2 seconds between reversals to extend motor life.
9. Watch for issues like unusual shaking, high temperatures, or odd sounds while working. Stop immediately to check if you notice anything unusual.
10. Addressing small issues prevents bigger ones. Understanding and caring for equipment reduces damage, costs, and delays.