Excavator use Juxiang S500 Sheet Pile Vibro Hammer
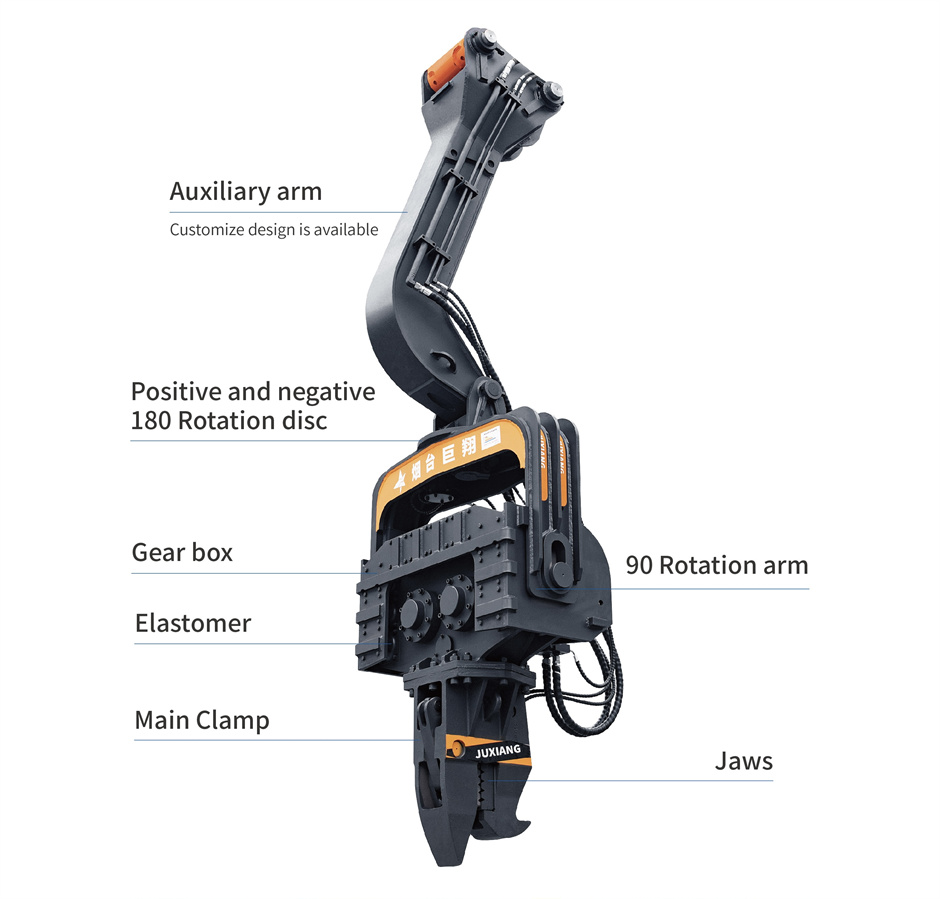
S500 Vibro Hammer Product parameters
Parameter | Unit | Data |
Vibration Frequency | Rpm | 2600 |
Eccentricity Moment Torque | N.M | 69 |
Rated excitation force | KN | 510 |
Hydraulic system pressure | MPa | 32 |
Hydraulic system flow rating | Lpm | 215 |
Max Oil Flow of Hydraulic System | Lpm | 240 |
Maximum pile length | M | 6-15 |
The auxiliary arm weight | Kg | 800 |
Total Weight | Kg | 1750 |
Suitable Excavator | Tons | 27-35 |
Product advantages
1. **Versatility:** Used on 30-ton excavator, positioned in the middle range of tonnages, can handle various scales of construction tasks, from small to medium-sized projects.
2. **Flexibility:** Medium-sized excavators like the 30-ton model are often more flexible than their larger counterparts, making them suitable for operations in confined spaces and enabling easy adjustments.
3. **Productivity:** In comparison to smaller excavators, a 30-ton excavator is more efficient in handling larger materials and tasks. It is also more maneuverable in tight spaces compared to larger excavators.
4. **Fuel Efficiency:** Generally, a 30-ton excavator offers better fuel efficiency compared to larger models, while still delivering efficient performance for larger projects.
5. **Cost-Effectiveness:** Both the purchase and operational costs of a medium-sized excavator are typically lower than those of larger models, providing good cost-effectiveness across a variety of projects.
6. **Moderate Digging Depth and Power:** A 30-ton excavator usually possesses moderate digging depth and digging power, making it suitable for most medium-scale excavation tasks.
Design advantage
Design Team: We have a design team of over 20 people, utilizing 3D modeling software and physics simulation engines to evaluate and improve the performance of products during the early stages of design.
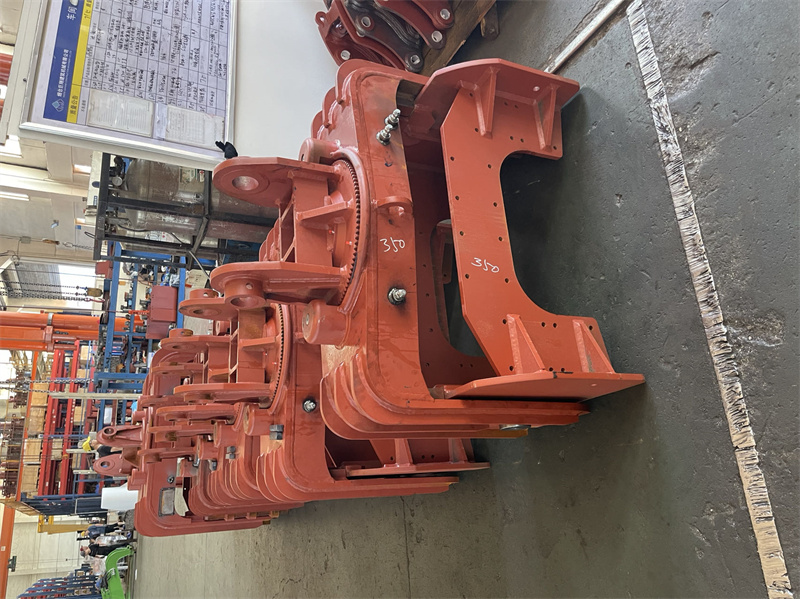
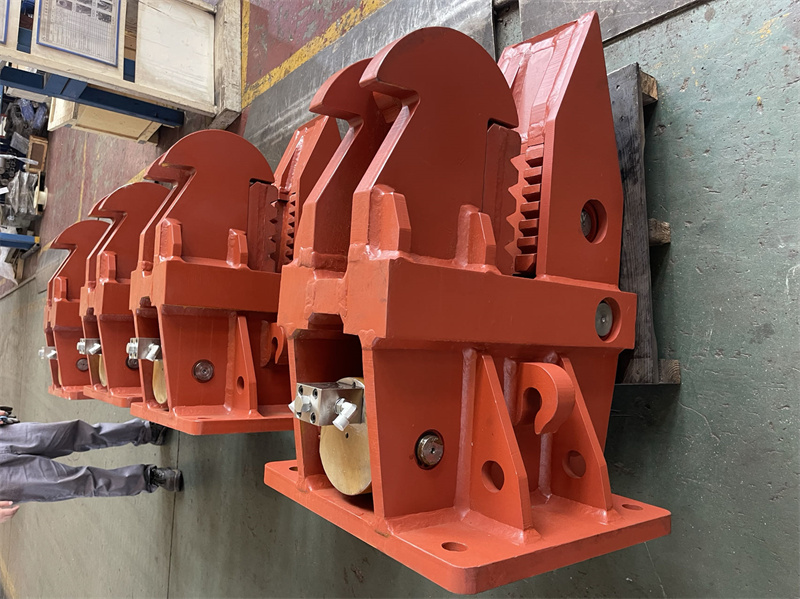
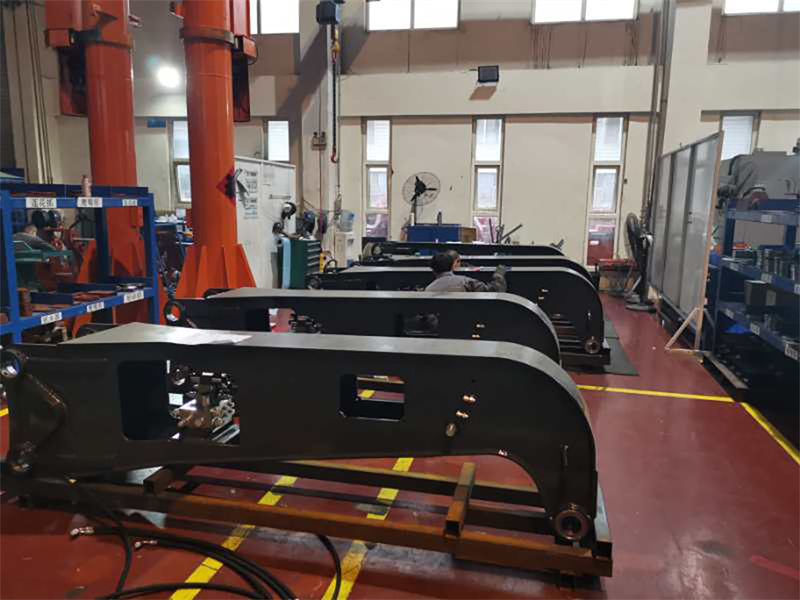
product display
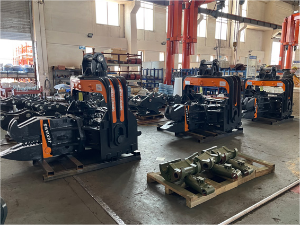
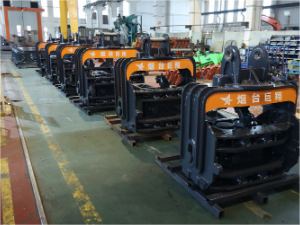
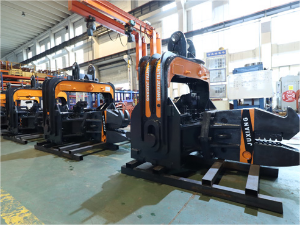
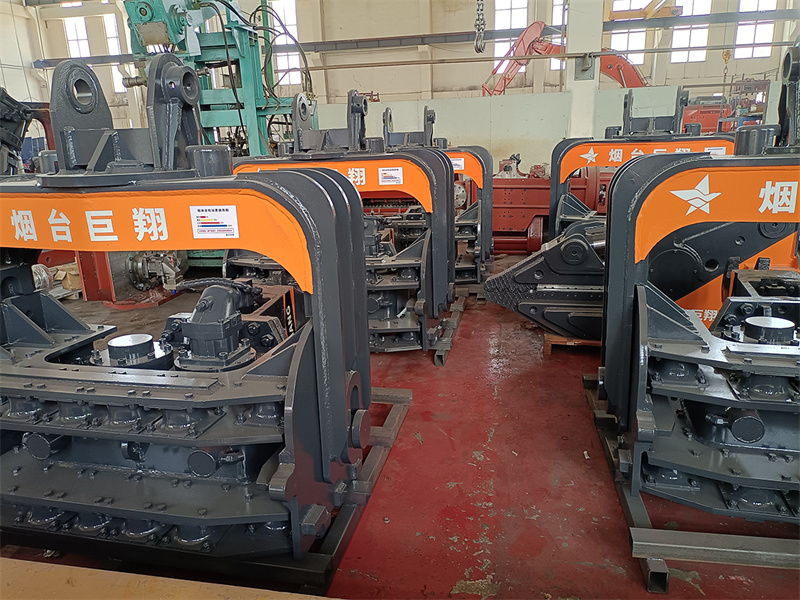
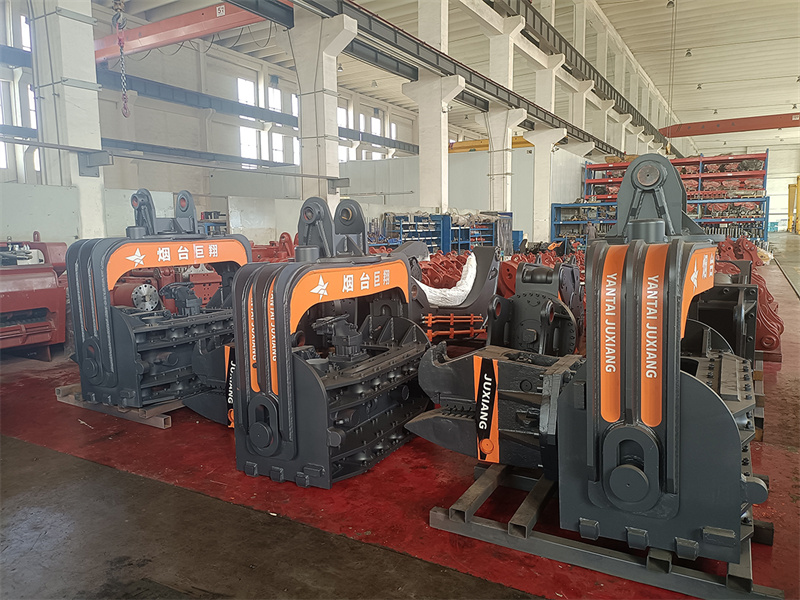
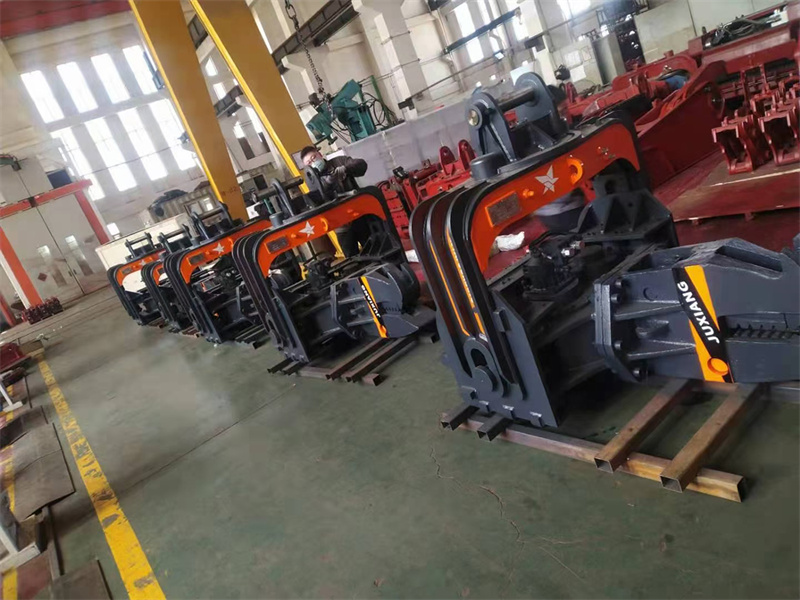
Applications
Our product is suitable for excavators of various brands and we have established long-term and stable partnerships with some well-known brands.
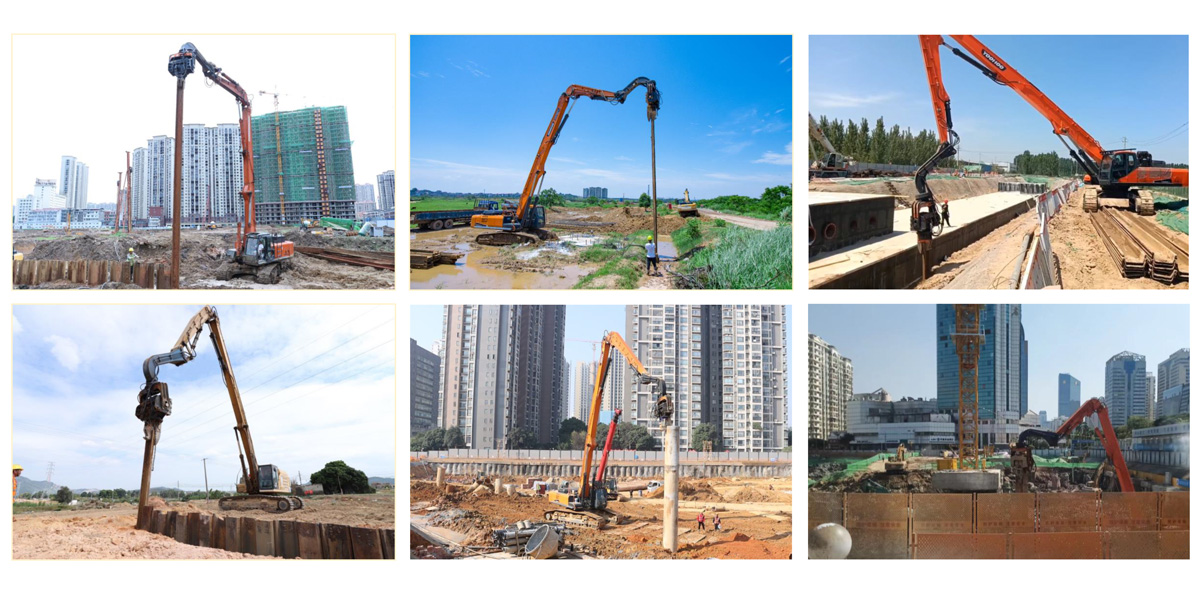

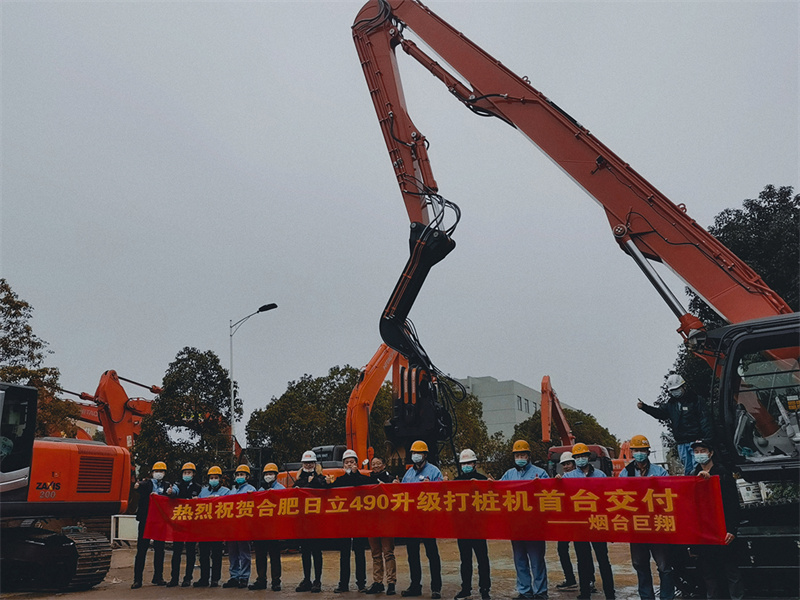
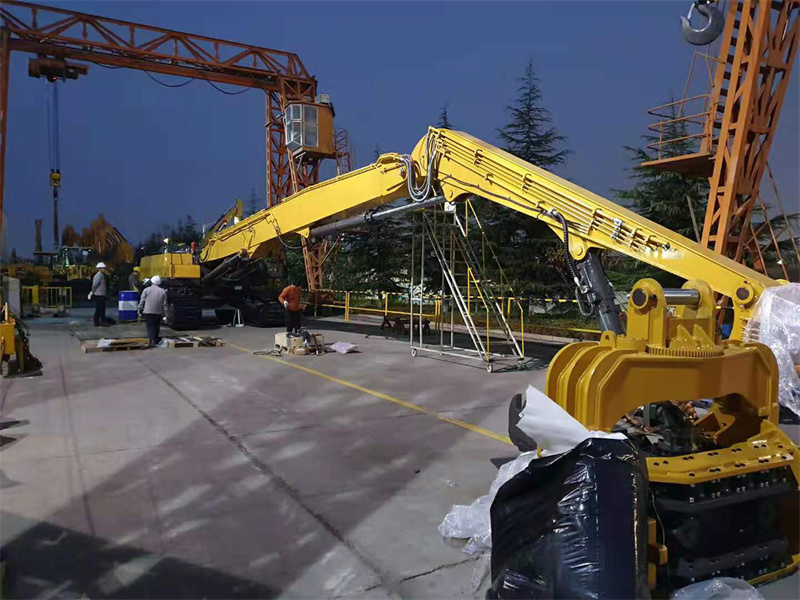
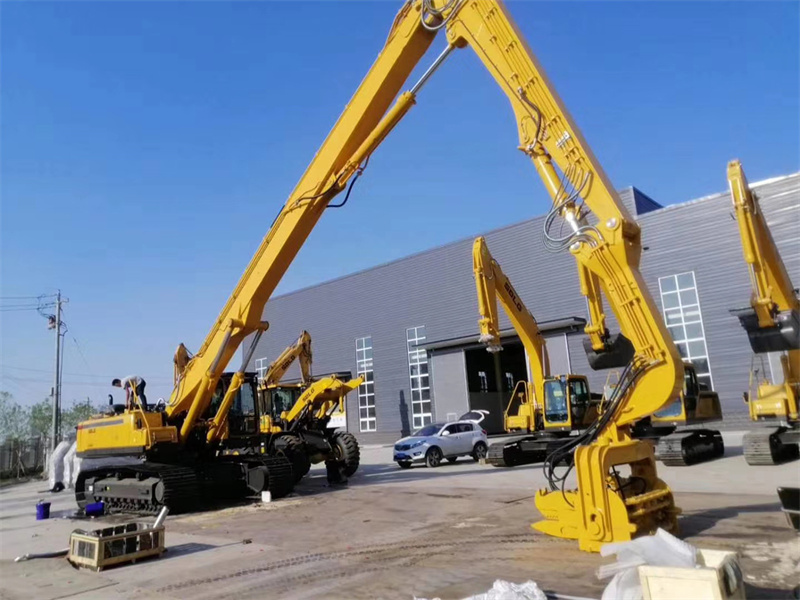
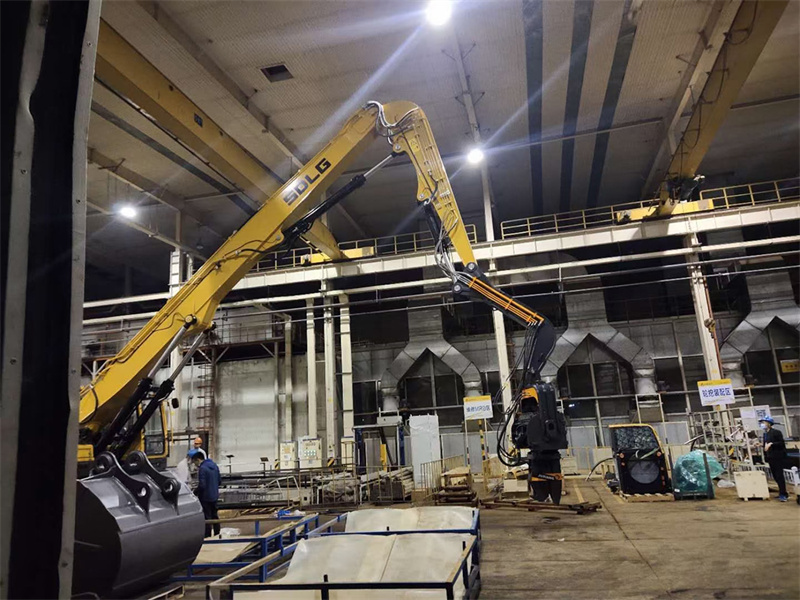
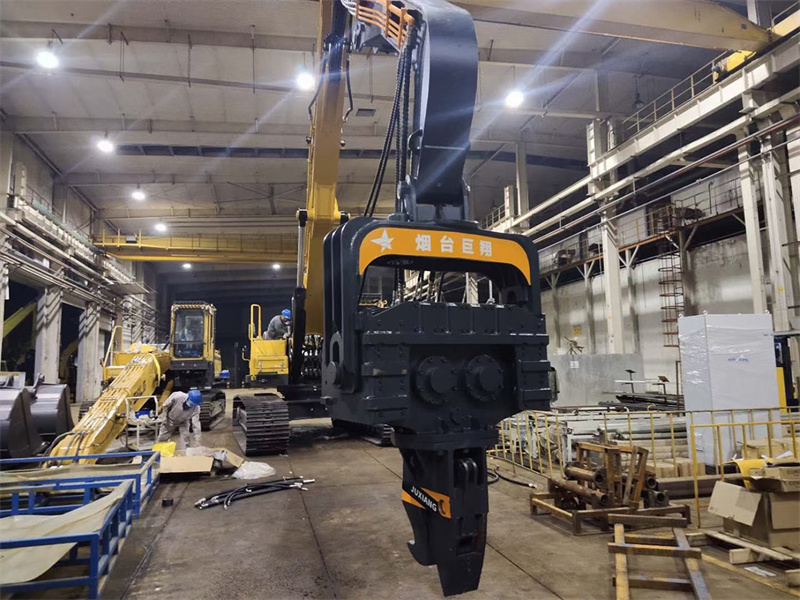
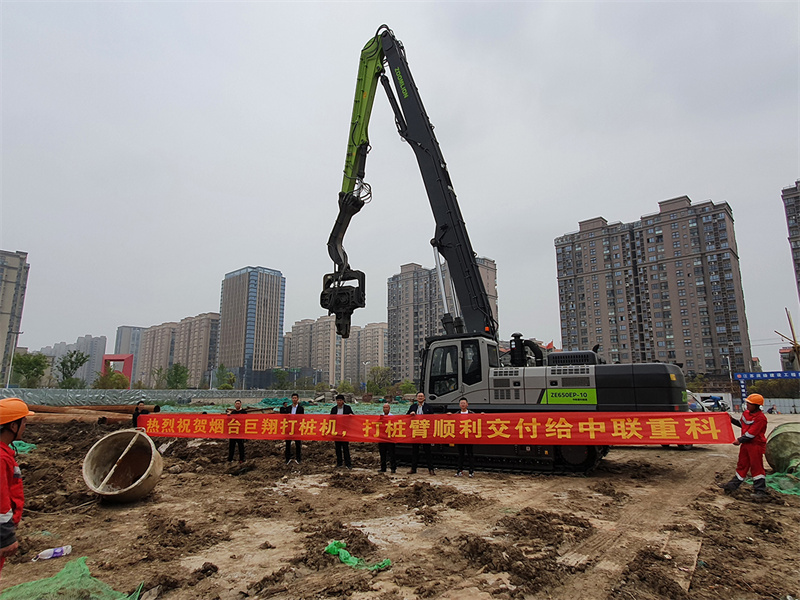
Also Suit Excavator: Caterpillar, Komatsu, Hitachi, Volvo, JCB, Kobelco, Doosan, Hyundai, Sany, XCMG, LiuGong, Zoomlion, Lovol, Dooxin, Terex, Case, Bobcat, Yanmar, Takeuchi, Atlas Copco, John Deere, Sumitomo, Liebherr, Wacker Neuson
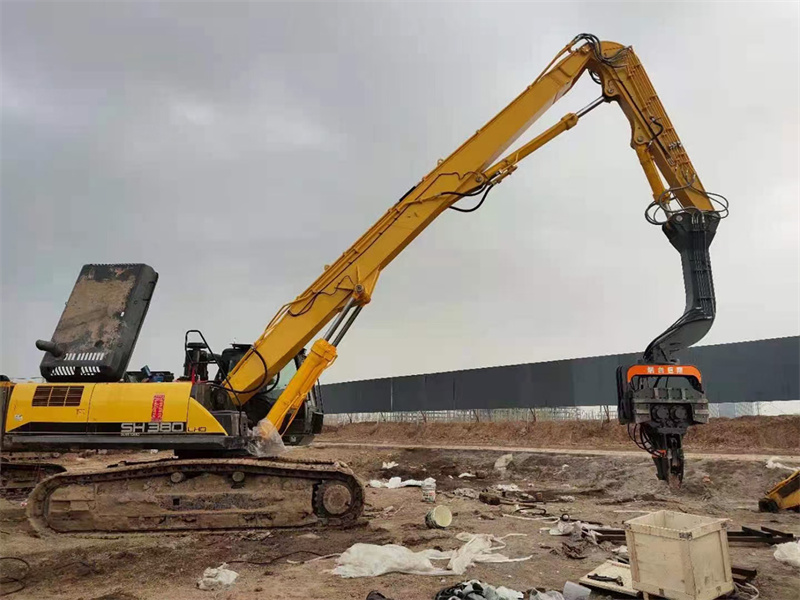
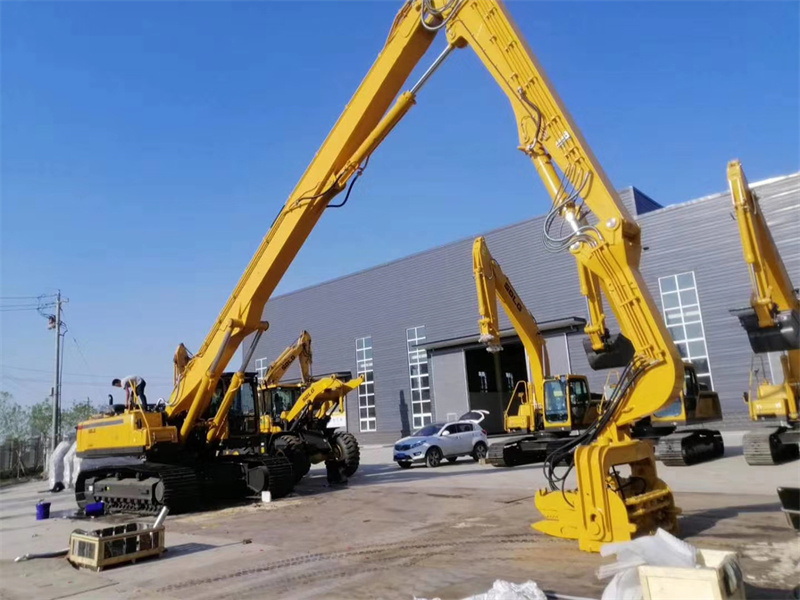
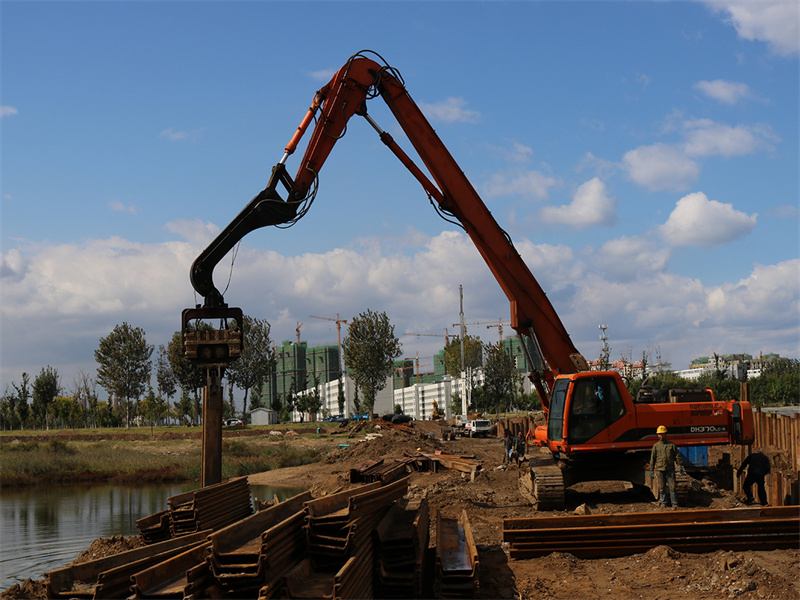
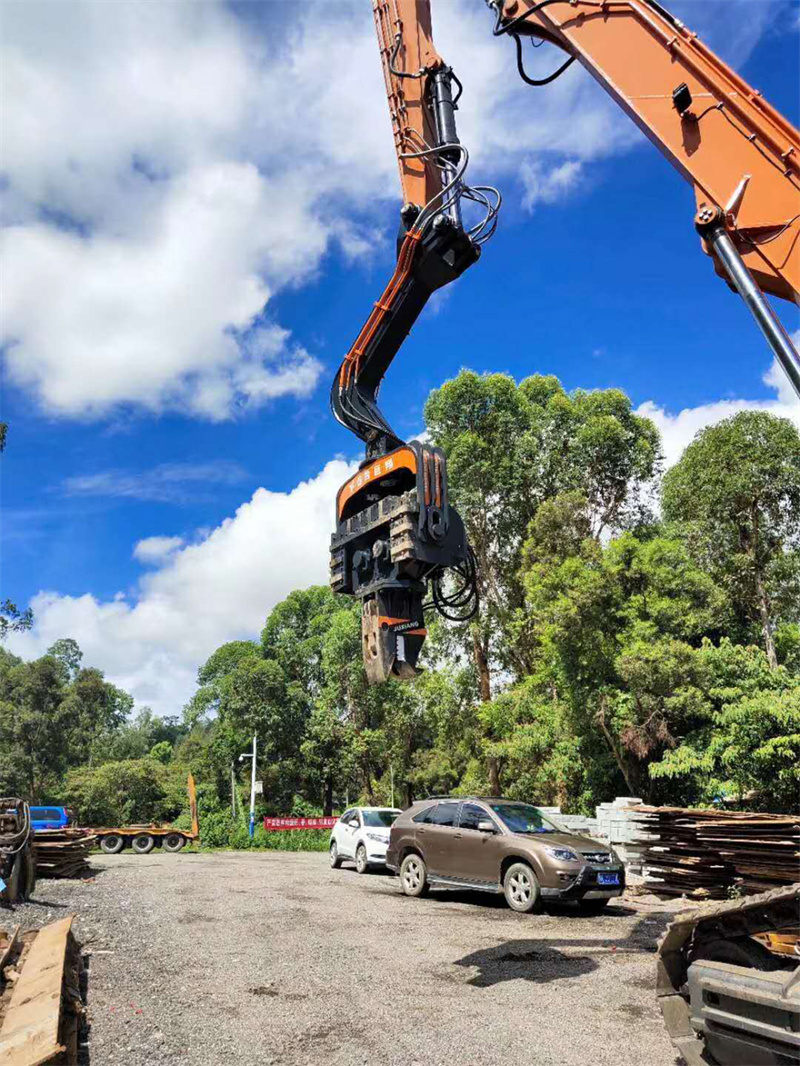
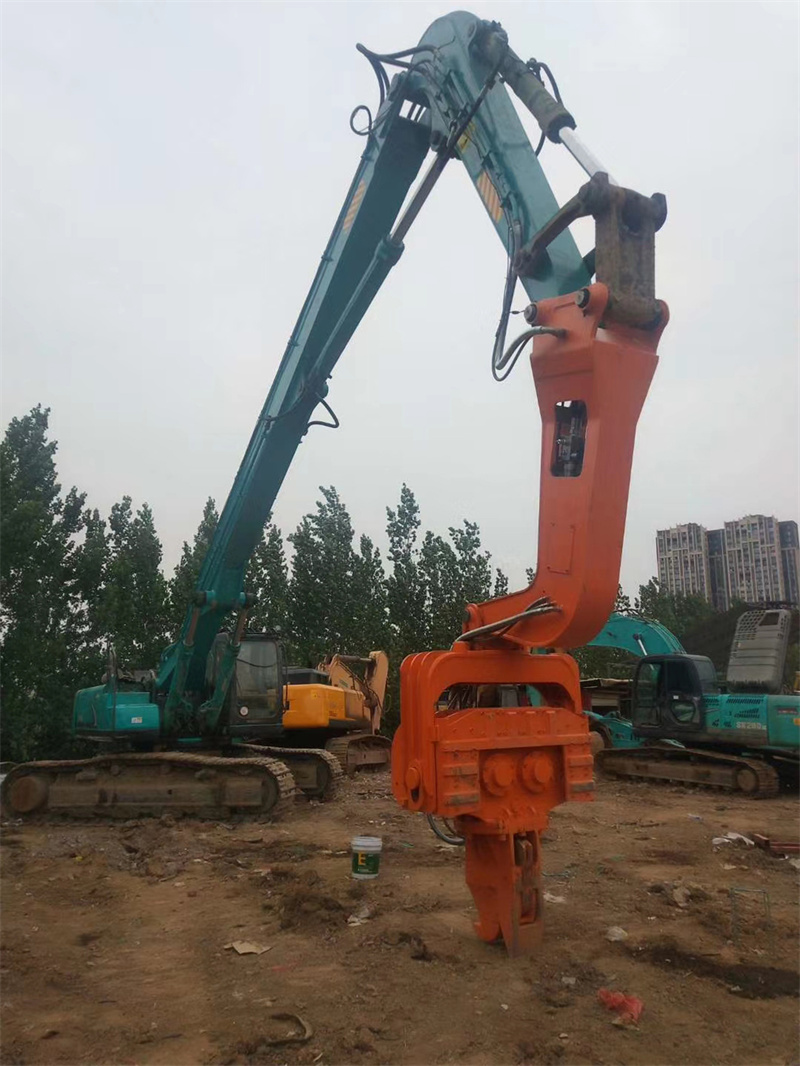
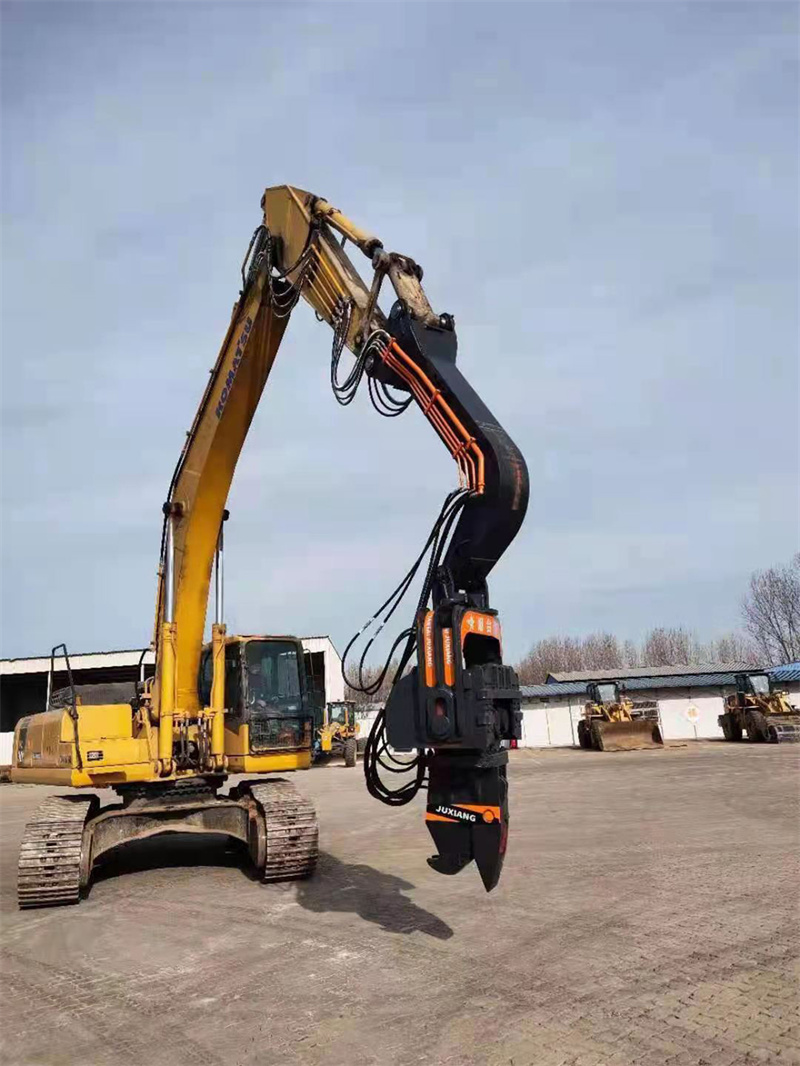
About Juxiang
Accessoryname | Warrantyperiod | Warranty Range | |
Motor | 12 months | During the initial 12 months, the replacement of a cracked shell and broken output shaft is provided without any cost. However, any incidents of oil leakage beyond the 3-month timeframe are excluded from claim coverage. In such cases, the responsibility of purchasing the necessary oil seal rests with the individual. | |
Eccentricironassembly | 12 months | The rolling element and the track stuck and corroded are not covered by the claim because the lubricating oil is not filled according to the specified time, the oil seal replacement time is exceeded, and the regular maintenance is poor. | |
ShellAssembly | 12 months | Damages caused by non-compliance with operating practices,and breaks caused by reinforce without the consent of our company,are not within the scope of claims.If Steel plate cracks within 12 months,the company will change the breaking parts;If Weld bead cracks,please weld by yourself.If you are not capable to weld,the company could weld for free,but no other expenses. | |
Bearing | 12 months | The damage caused by poor regular maintenance, wrong operation, failure to add or replace gear oil as required or is not within the scope of claim. | |
CylinderAssembly | 12 months | If the cylinder barrel is cracked or the cylinder rod is broken, the new component will be replaced free of charge. The oil leakage occurring within 3 months is not within the scope of claims, and the oil seal must be purchased by yourself. | |
Solenoid Valve/throttle /check valve /flood valve | 12 months | Claims do not encompass instances where coil short-circuiting results from external impacts or incorrect positive and negative connections. | |
Wiring harness | 12 months | The short circuit caused by external force extrusion, tearing, burning and wrong wire connection is not within the scope of claim settlement. | |
Pipeline | 6 months | Damage caused by improper maintenance, external force collision, and excessive adjustment of the relief valve is not within the scope of claims. | |
Bolts, foot switches, handles, connecting rods, fixed teeth, movable teeth and pin shafts are not guaranteed; The damage of parts caused by failure to use the company’s pipeline or failure to comply with the pipeline requirements provided by the company is not within the scope of claim settlement. |
1. During the installation of a pile driver onto an excavator, ensure that the hydraulic oil and filters of the excavator are replaced following installation and testing. This practice guarantees the seamless operation of the hydraulic system and the pile driver’s components. It’s crucial to prevent any impurities that could potentially damage the hydraulic system and diminish the equipment’s longevity. Please note that pile drivers demand rigorous standards from the excavator’s hydraulic system. Thoroughly inspect and rectify any issues before installation.
2. Newly acquired pile drivers require an initial break-in period. For the first week of usage, change the gear oil after approximately half a day to a full day’s work, and subsequently, every three days. This translates to three gear oil changes within a week. Following this period, perform regular maintenance based on the accumulated working hours. It’s recommended to change the gear oil every 200 working hours (while avoiding surpassing 500 hours). This frequency is adaptable according to your workload. Additionally, remember to clean the magnet each time you conduct an oil change. A vital note: do not exceed intervals of 6 months between maintenance checks.
3. The magnet inside primarily serves as a filter. During pile driving operations, friction generates iron particles. The magnet’s role is to attract and retain these particles, effectively maintaining the cleanliness of the oil and reducing wear. Regular cleaning of the magnet is crucial, recommended approximately every 100 working hours, with flexibility based on operational intensity.
4. Before commencing work each day, initiate a warm-up phase for the machine, spanning around 10 to 15 minutes. As the machine remains idle, oil tends to accumulate at the lower parts. Upon startup, the upper components initially lack proper lubrication. After approximately 30 seconds, the oil pump begins circulating oil to the necessary areas, effectively minimizing wear on components such as pistons, rods, and shafts. Utilize this warm-up phase to inspect screws, bolts, and to apply grease for proper lubrication.
5. When driving piles, employ restrained force initially. Increased resistance calls for heightened patience. Gradually drive the pile into the ground. If the first level of vibration proves effective, there’s no immediate need to switch to the second level. While the latter may expedite the process, increased vibration also accelerates wear. Whether utilizing the first or second level, in situations of slow pile progress, carefully withdraw the pile by approximately 1 to 2 meters. This harnesses the combined power of the pile driver and excavator to achieve deeper penetration.
6. Following pile driving, allow a 5-second interval before releasing the grip. This practice significantly reduces wear on the clamp and other associated parts. Upon releasing the pedal following pile driving, due to inertia, all components remain tightly engaged. This minimizes wear. It’s advisable to release the grip when the pile driver comes to a halt in vibration.
7. The rotating motor is designed for pile installation and removal purposes. However, refrain from utilizing it to rectify pile positions caused by resistance or twisting forces. The combined effect of resistance and the pile driver’s vibration exceeds the motor’s capacity, leading to potential damage over time.
8. Reversing the motor during instances of over-rotation subjects it to stress, resulting in potential damage. It’s advisable to introduce a brief 1 to 2-second pause between motor reversals. This practice mitigates strain on the motor and its components, effectively extending their operational lifespan.
9. While in operation, remain vigilant for any irregularities, such as unusual shaking of oil pipes, elevated temperatures, or abnormal sounds. In the event of detecting anomalies, immediately cease operation to investigate. Addressing minor issues in a timely manner can effectively prevent more significant problems from developing.
10. Neglecting minor issues can lead to substantial consequences. Recognizing and properly maintaining equipment not only mitigates damage but also minimizes costs and delays.